Local Storage seems to be disabled in your browser.
For the best experience on our site, be sure to turn on Local Storage in your browser.
How Are Coins Made?
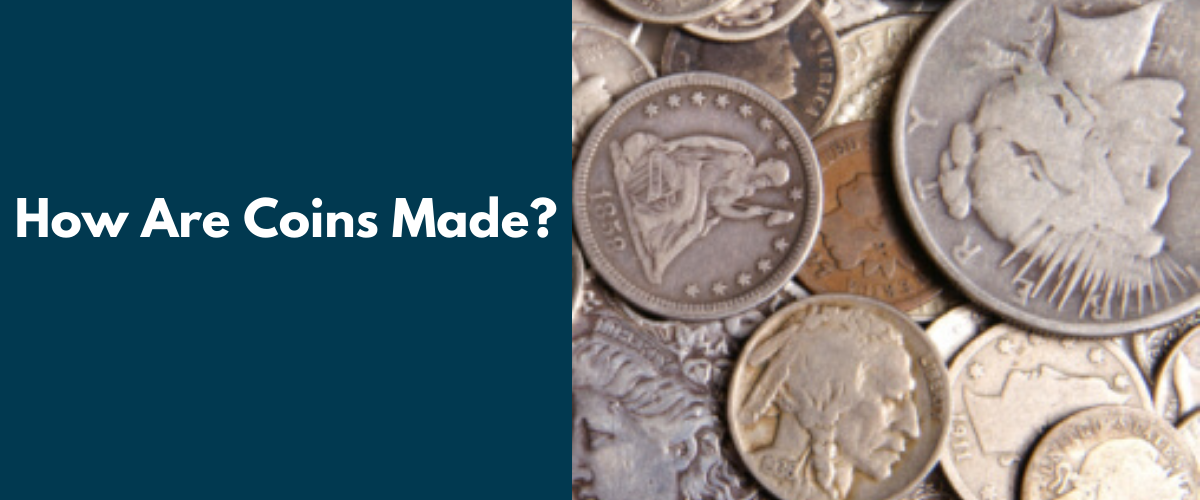
The average American citizen doesn't put too much thought into how their pocket change is made. However, coin collectors and numismatists are very interested in the minting process. So, assuming you hope to advance in the numismatic community – or maybe you just want to gain some interesting facts to surprise your friends with – you should learn more about how coins are made. Here are some key terms to remember before you begin:
- Minting: process of creating coins
- Coin die: one of the metallic pieces that strike each side of the coin
- Striking: method of pressing an image into the blank metal using a coin die
The minting process of coins has been around for thousands of years – since around 700 B.C. There have been hundreds of different minting techniques and technologies over the years, along with many different leaders' and prominent figures' images gracing the coins. Initially, coins were made with a hammer and anvil from scraps of metal. But with the evolution of technology, the coining process progressed to using screw and steam presses. Today, the most current and cutting-edge procedures are utilized. For example, both electric and hydraulic presses are used for minting today’s coinage.
Coin Production and the Minting Process
Designing the Coin
First, an artist develops images and designs for the coin to be created. The artist uses computer software to perfect the details, and then creates a large plaster model of the design, which is almost five times its original size! This task is incredibly difficult and can take weeks to complete, which is understandable considering the complexity of the designs and the need for them to be equally as intricate and defined on a much smaller scale.
Breaking the Mold
Once the plaster mold is complete, it is transferred to a rubber resin template (another mold), which is used to make an epoxy galvano. In this example, epoxy is essentially a casting made with adhesive properties, while galvano is the name of the epoxy model once it is sculpted and coated. Essentially, this process is changing melted rubber to silicone rubber, which is done when the rubber hardens in the new mold. The reason for first creating the design on a plaster and later transferring it onto a rubber mold is because plaster is easier for the artists to work with when engraving.
Creating the Master Die
Once the epoxy galvano is complete, it is sent through a reducing lathe with the use of a machine called a pantograph. This process shrinks an object to scale – and can take several days to complete. The pantograph traces the contour of the mold onto what will be the steel master die, which is the actual size of the coin to be struck. Multiple copies of the master die are made (called working dies) and will be used for the actual striking. Because of the intense pressure applied while striking a coin, the design eventually will wear off of the dies, which is why multiple working dies are made. This ensures that all of the coins are struck before all of the dies are worn off. Also, it's important to realize that two different dies are needed for each coin – one for the obverse (front) and one for the reverse (back). After this time-consuming step is complete, the process of reduction is done, and the coins are ready to be struck!
Time to Strike!
The precious metal to be struck is supplied to the mints in large, coiled strips, which are then cut into the correct size by a blanking press. Once the blanks are checked and properly cleaned, they are ready to be coined! The working dies are installed into specific minting machines based on their respective denominations, and then the blanks are fed into – what is lovingly called – the "Feeding Hopper." The amount of strikes and pressure a coin will receive is based off of the material used and the required finish. Proof blanks are fed by hand into the presses, because proof quality doesn't allow mass production. Also, some coins may receive a hand-painted finish after they are minted. After the minting process is complete, the coins receive a final inspection – and many times a grading by a third party before they are capsuled and packaged.
For further reading about graded coins, read this Coin Authority article.
So, the next time you're admiring your collection or waiting for a new coin to be released, take a moment to appreciate the amount of effort, time, and detail that went into creating that intricate piece of art.
© 2024 Copyright GovMint.com. All Rights Reserved. GovMint.com does not sell coins and numismatics as investments, but rather as collectibles. Please review GovMint's Terms and Conditions, Terms of Use and Privacy Policy before using this website and prior to purchasing from GovMint.com.